OPERATING MODEL
We focus on driving operational excellence at the factory level, reducing waste and steadily increasing efficiency. The resulting savings are invested in workers - through benefits, empowerment programs, and steady progress towards living wages.

We select African factory partners with aligned values and a vision for scale.
We support factories to continuously improve operations through training by our on-the-ground technical and compliance experts.
We support factories to continuously improve operations through training by our on-the-ground technical and compliance experts.
We support factories to continuously improve operations through training by our on-the-ground technical and compliance experts.
We ensure a portion of the profit from these orders is reinvested into workers - through benefits, empowerment programs, and making steady progress towards living wages.
We measure the resulting benefits in productivity (through decreased absenteeism / turnover), and continue to support factories to improve, grow, and create jobs.
We deliver high quality, cost competitive, and ethically manufactured product for our clients.
We deliver high quality, cost competitive, and ethically manufactured product for our clients.
We manage volume orders from our US/EU/UK partners from product development to ex country, enabling factories to increase efficiency.
Our passionate, experienced team drives this Operating Model forward on the ground in Ghana and Benin. Read more about our people here.
Building the industry we want
The frontier of apparel manufacturing is shifting to Africa, bringing with it opportunity to create millions of jobs for women but also risk of repeating these patterns of exploitation. West Africa has the potential to be different.
We founded Ethical Apparel Africa with the vision of shaping the industry in Ghana to ‘get it right from the start’. We work with local women-owned factories and support them to make the leap to export while prioritizing the well being of their workers. To do this, we leverage technology and lean management to create a virtuous cycle of productivity and investment in people.
We are on a mission to empower people and protect the planet. By 2030, we aim to create 10,000 sustainable jobs, over 70% for women.
In 2021 EAA invested to acquire Maagrace Garment Industries Ltd, a factory in Koforidua, Ghana, and quickly created 500 jobs, making us now the second largest garment factory in Ghana. We have developed Maagrace as a 'Model Factory' with a learning lab approach and opened ourselves up to the wider industry. Our decisions are driven by data, and focused on creating model operations for impact in four key areas:
Gender Equity
-
We train women in high-skill, traditionally male areas (mechanics, digital patterns, cutting)
-
We are working to increase % of women in management (currently above 45%; goal to increase to 70%),
-
Women have a strong voice on democratic worker committees
-
We offer dignified, fair, well-compensated employment with extensive benefits that center women’s experiences and needs
A
Fair Compensation
-
We undertook a detailed research project to triangulate an accurate living wage, surveying 150+ people using the Poverty Probability Index (PPI) and a cost-of-living survey tool developed with support from the Ethical Trading Initiative.
-
Our survey confirmed that we’re in range of a living wage for the area. We are committed to continuing to raise wages and share best practices with other factories in the region.
Worker wellbeing & empowerment
-
At the center of our impact process lies asking workers what they need to improve their lives. Based on their input, we have implemented health, and education programs (SRH, Malaria prevention, WASH) as well as digital literacy training
-
Beyond wages and benefit/empowerment programs, we care about how people feel coming to work each day – the intangibles of whether it’s a ‘best place to work’. To measure this, we launched a 3 year wellbeing initiative in partnership with the Levi's Foundation.
Climate solutions
-
As Ghana's largest solar-powered garment factory, we have avoided over 150K kg in CO2 emissions and are actively supporting others to go green
-
To move the needle on up-cycling / re-cycling, we launched a waste reduction task-force with strong engagement from workers
-
We are pushing for a circular economy ecosystem vision – secondhand clothes to fiber to garment – in West Africa. Combined with our direct shipping route to the US, this supply chain could drive huge carbon savings.
Worker stories

Meet Bernice Gabienu
Bernice was initially recruited as a trainee machinist in July 2019. After only 3 months, Bernice was not only able to carry out basic sewing operations, but she had learnt how to repair sewing machines. Bernice was therefore promoted as Mechanic Supervisor. Bernice is in charge of a team and oversees an automated needle issuance and recording system.
“I knew I wanted to be a mechanic the moment I was recruited as a trainee. Many of my friends initially tried to discourage me for my choice of a male dominated area. But I love my job as a mechanic and it fills me with pride whenever I am able to fix a problem on a machine" Bernice said.

Meet Olivia Vanessa Kornutse
Olivia who is only 21 years old, has been working as a single needle Operator for 2 years. Through the multi skilling training she followed, Olivia has learnt new operations and now uses single needle machines for zip attachment, double needle machines for bottom and sleeve heming, as well as overlock machines. Thanks to the new skills acquired, Olivia has been promoted to a grade A operator (highest grade) and then to a supervisor role.
"I am happy I have demonstrated my capacity to grow. I know that my peers respect me a lot. In addition, I have been appointed as the new Gender Champion. I am so grateful and proud to represent my peers and represent all women in the factory. I feel I am on a mission and want all women to follow their dreams and grow as well", Olivia Vanessa shared.

Meet Theresa Dartey
Theresa started her career as a hairdresser before she decided to work in the apparel manufacturing. Without any initial skills, she applied in December 2019 and, after following a rigorous recruitment process was hired as a Trainee Operator. Theresa was able to learn rapidly and demonstrated real leadership skills. She was then promoted from Operator to Line Supervisor.
“My transition from an operator to an operator supervisor has truly been a blessing for me and my family. Apart from the prestige that comes with my new position, my monthly salary has more than doubled and I am very grateful for that", Theresa said.
our contribution towards the SDGs
Through our commitment to ethical manufacturing and to catalysing the sustainable growth of the apparel sector in West Africa, we are making meaningful progress towards many of the UN Sustainable Development Goals in particular the following --
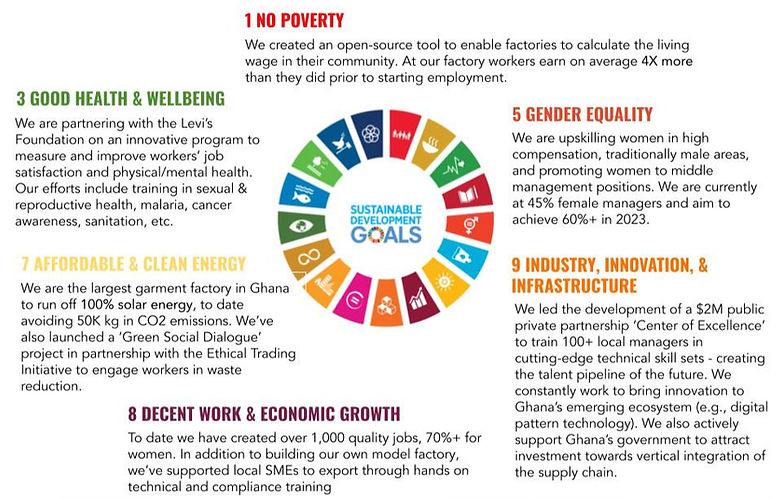
BEYOND COMPLIANCE
We believe compliance should be a process of continuous and sustainable improvement, not an exercise in tick boxes and one-off audits. For us, compliance is only the starting point and should not replace a rigourous due diligence approach that applies at every operational level.
As stated above, we are developing our partner factories to sustainably implement living wages, benefits, and empowerment programs to increase workers’ satisfaction and wellbeing. It’s the right thing to do, and it’s also good for business - leading to lower staff turnover, reduced absenteeism, and better productivity. We are partnering with the UNDP Business Call to Action and the UN Foundation to assess and measure our Impact initiatives.
We are a proud signatory of the Social & Labor Convergence Project (SLCP), a coalition of brands and suppliers focused on developing a converged global assessment to reduce audit fatigue and redirect resources towards improving workers’ lives. We are also contributing to the Ethical Trading Initiative (ETI) NGO Caucus to support best coalitions, frameworks and strategies to promote workers rights and fair purchasing practices around the world.
Our partner factories have successfully completed SEDEX/ Smeta audits, GRS and/or WRAP audits. They all commit to complete transparency towards continuous improvement on compliance. Our on the ground team continuously works with partners to ensure compliance policies and procedures are enforced at all time and beyond compliance programs are implemented with monitoring and evaluation frameworks. We also conduct rigorous formal assessments against our Social Compliance Improvement tool, which integrates input from a range of standards (ILO, ETI, SMETA, WRAP, SA8000, BSCI, Higg) into 100+ criteria with 4 phases. These assessments are shared with our clients on a regular basis and periodically validated by external bodies.
EAA has zero tolerance for any form of forced labor, and alll our partner factories adhere to the Ethical Trading Initiative (ETI) Base Code. In accordance with the UK Modern Slavery Act, we have developed a formal statement specifying our commitment to implementing and monitoring policies, procedures and continuous training across our factory network. Click here to read our statement.
EAA Foundation
The EAA Foundation (EAAF) is a US 501c3 non profit organization with a mission to provide startup support for sustainable programs to increase wellbeing and empowerment for workers in garment factories in Africa.
EAAF's Board of Trustees funds programs based on their alignment with the Foundation's Guiding Principles, which include: putting workers first and listening to what they say they need; ensuring women are the core recipients of funded programs; prioritizing sustainability and shared responsibility with factories applying for funds; and seeking to make a measurable difference in workers' lives.
EAAF is currently accepting donations for a special 'Containers of Hope Campaign'. As a result of a cancelled order, EAA has a stock of US-grade medical scrubs. With donor support, EAA will be able to donate these products to front-line medical workers delivering vital medical services in conflict zones around the world. Each container will transport 8,000 sets of medical scrubs and ships for $25K. Any donations made will have a double impact -- facilitating shipment of vital medical scrubs while also providing support to garment worker empowerment programs.
Donations can be accepted via Stripe here, and also via direct bank transfer at the following details:
Wells Fargo Bank
Account #: 5123339151
Routing # for International Wire Transfers (SWIFT code): WFBIUS6S
Routing # for Domestic Wire Transfers: 121000248
